Krig er kendt for at være den bedste fremdriftsmotor. Tankindustrien i Sovjetunionen gjorde et svimlende kvalitativt spring på få krigsår. Den sande krone på dette var kampvognene i IS -serien.
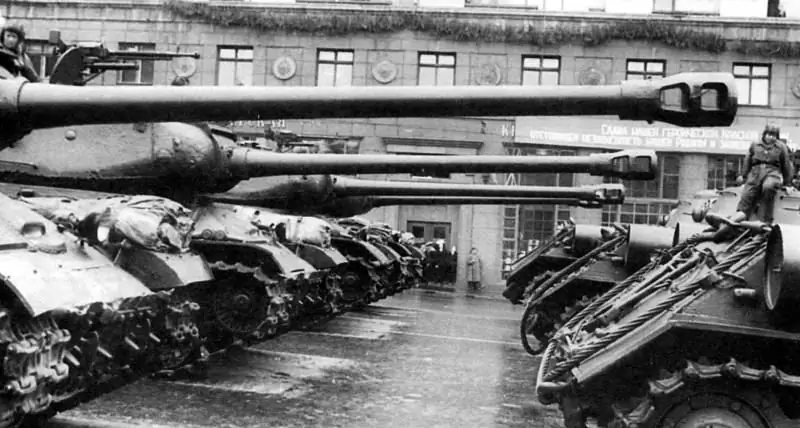
Magnitogorsk opskrifter
I den foregående del af historien handlede det om den 70L støbte rustning med høj hårdhed, der blev brugt til tårne i IS-kampvognene. Panserudviklerne fra TsNII-48 var langt fra den første erfaring med at skabe beskyttelse til tunge tanke.
Før Kursk Bulge, som blev en katalysator for udviklingen af indenlandske tunge tankbygninger, var hovedformålet med modernisering KV -tanken. Oprindeligt var alt arbejde rettet mod at reducere andelen af knappe legeringsadditiver i rustningens sammensætning. Selv navnet i TsNII -48 kom med et passende navn - økonomisk legeret stål. Den originale rustning af mærket FD-7954, hvormed KV-tanken gik ind i den store patriotiske krig, indeholdt ifølge tekniske krav op til 0,45% molybdæn, 2,7% nikkel og krom.
I slutningen af 1941 skabte en gruppe forskere under ledelse af Andrei Sergeevich Zavyalov ved det pansrede institut en opskrift på stål FD -6633 eller 49C, hvor molybdæn ikke krævede mere end 0,3%, chrom - op til 2,3%og nikkel - op til 1, 5%. I betragtning af at KV -seriens tanke fra anden halvdel af 1941 til 1943 blev samlet omkring 4 tusind eksemplarer, kan man forestille sig mængden af reelle besparelser i legeringsmetaller.
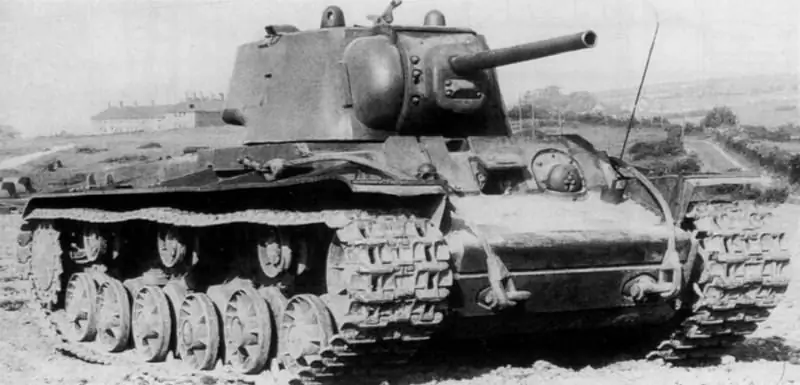
Hemmeligheden bag succes
Hemmeligheden bag metallurgernes succes ligger i undersøgelsen af parametrene for dannelsen af fibrøst brud på rustning - hovedparameteren for projektilmodstand. Det viste sig, at du kan undvære en betydelig del af legeringselementer ved blot at ændre rustningens kølehastighed under slukning. Men dette er enkelt i ord - hvor mange indledende eksperimenter og smelter metallurger måtte lave, er det kun de nu klassificerede arkiver, der vil kunne fortælle.
På Magnitogorsk Metallurgical Plant i 1941 blev de første prototyper af 49C stål opnået, som ikke var ringere end den traditionelle "førkrig" rustning. Især beskydningen af 76 mm kanonen viste fuld overensstemmelse med de taktiske krav til tanken. Og siden 1942 blev kun rustning med navnet 49C brugt til KV -serien. Det er værd at huske, at forbruget af chrom, molybdæn og nikkel er faldet betydeligt.
Søgningen efter nye rustningsformuleringer til tungt udstyr sluttede ikke der. I 1942 blev stål GD-63-3 "svejset", fuldstændig blottet for knappe krom og nikkel. Til en vis grad blev nikkel erstattet af mangan - dets andel steg mere end tre gange (op til 1,43%). Prototyper af den nye rustning blev affyret. Og de viste sig at være ganske egnede til massebrug i designet af KV. Men Klim Voroshilov -kampvognene med rustning af medium hårdhed trak sig tilbage. Og stedet for tunge køretøjer blev indtaget af "Joseph Stalin" -køretøjer med rustning med høj hårdhed.
Valset rustning 51C
Hvis 70L rustningen til IS-2 tårnet kunne støbes, fungerede dette trick ikke med tankens skrogdele. Her stod ingeniører over for to problemer på én gang - skabelsen af rustninger med høj hårdhed af stor tykkelse og behovet for at svejse den ind i et færdigt skrog.
Alle, der er interesseret, er sandsynligvis allerede klar over de problemer, der skyldes svejsning af T -34 -rustningen - der er stor sandsynlighed for revner i svejseområdet. IS-2 var ingen undtagelse. Og dens krop skulle oprindeligt være kogt af endelig varmebehandlede dele.
I erkendelse af hvilke vanskeligheder og farer en sådan teknologisk løsning ville bringe i militær operation, ændrede TsNII-48-specialister tankproduktionscyklussen. Som et resultat, i 1943, på Ural Heavy Machine Building Plant og Chelyabinsk-anlægget nr. 200, blev IS-2-skroget besluttet at blive kogt af rustningsplader, der kun havde passeret en høj ferie efter rullning. Det er faktisk, at skroget på en tung tank var samlet af "rå" stål. Dette reducerede kraftigt svejsefejl på 51C rullet rustning med høj hårdhed.
Den endelige varmebehandling ved opvarmning før afkøling blev allerede udført på tankens svejsede legeme efter tidligere at have styrket den med interne stivere. Kroppen blev opbevaret i ovnen i tre timer. Og derefter, på specielle enheder, blev de overført til en vandslukkende tank og opbevaret i den i 15 minutter. Desuden steg vandtemperaturen i slukningstanken fra 30 til 55 ° C. Kroppens overfladetemperatur efter at være blevet fjernet fra vandet var 100–150 ° С. Og det er ikke alt.
Efter slukning blev kroppen straks udsat for lavt temperering i en cirkulerende ovn ved en temperatur på 280-320 ° С med standsning efter at have nået denne temperatur i 10-12 timer. Den lave temperering af støbte tårne fra 70L rustning blev udført på en lignende måde. Interessant nok varede revneregulering i de eksperimentelle IS-2 skrog i fire måneder, da de første produktionstanke forlod fabriksportene.
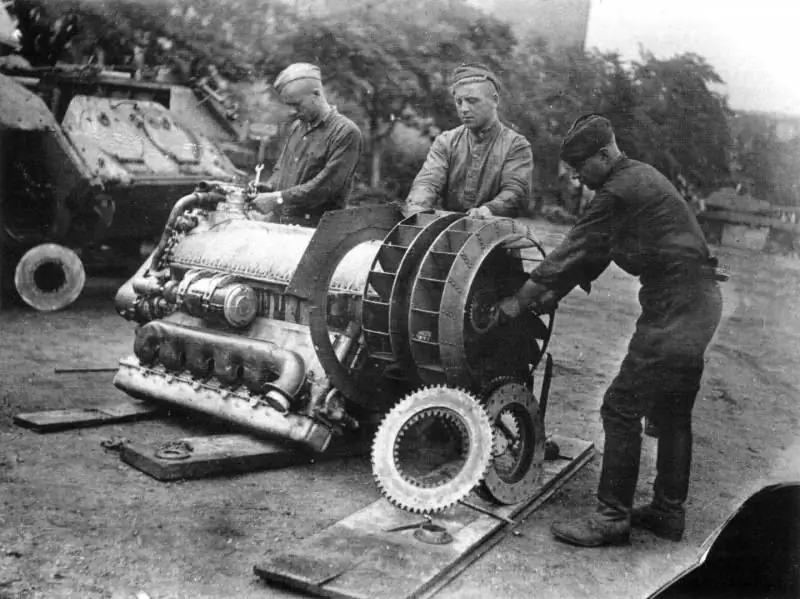
Kemisk sammensætning
Hvad var den 51C rullede rustning, der blev den vigtigste for IS-2, ISU-122 og ISU-152? Det er et dybt hærdet stål til store rustningstykkelser med følgende kemiske sammensætning (%):
C 0, 18–0, 24
Mn 0, 70–1, 0
Si 1, 20–1, 60
Cr 1, 0–1, 5
Ni 3,0-3,8
Mo 0, 20–0, 40
P ≤ 0,035
S ≤ 0,035.
I sammenligning med den støbte rustning 70L havde 51C -valset stål en højere andel molybdæn og nikkel, hvilket garanterede en stigning i hærdeevnen op til 200 mm. Da skrogene på tunge tanke blev affyret med 88 mm skaller, viste det sig, at rustningen med høj hårdhed var langt bedre i holdbarhed end sine forgængere med medium hårdhed. Spørgsmålet om at placere rullet rustning 51C blev løst med det samme.
Smart svejsning
Et vigtigt bidrag til succesen med udviklingen af rustningsproduktion af tanke i IS -serien blev givet ved automatisk svejsning af stål under et lag af flux. Da det var umuligt at overføre hele processen med fremstilling af et tankpansret skrog til sådan svejsning i begyndelsen af 1944, fokuserede ingeniørerne på at automatisere de mest forlængede og mekanisk belastede sømme.
På fabrikken i Chelyabinsk nr. 200, under samlingen af skroget på IS-2 tunge tank, kunne kun 25% af alle svejsninger automatiseres. I midten af 1944 var Tankograd i stand til at automatisere 18% af alle mulige 25% af svejsninger. Den samlede længde af de svejsede sømme langs skroget på IS-2 tunge tank var 410 løbende meter, hvoraf 80 løbende meter blev udført ved den automatiserede svejsemetode.
Dette resultat har ført til betydelige besparelser i knappe ressourcer og elektricitet. Det var muligt at frigøre op til 50 kvalificerede manuelle svejsere (deres arbejdsomkostninger i mængden af 15.400 arbejdstimer) og spare 48.000 kilowattimer elektricitet. Nedsat forbrug af elektroder (ca. 20.000 kg, austenitisk - 6.000 kg), ilt (med 1.440 kubikmeter).
Tiden til svejsning er også reduceret betydeligt. F.eks. Tog svejsning af bunden og tårnboksen til siderne med en seksten meters søm 9,5 arbejdstimer i manuel tilstand, og kun 2. En søm med lignende længde forbinder bunden til siderne af tankskroget i automatisk tilstand påkrævet 3 arbejdstimer (i manual straks 11, 4). Samtidig kunne højtuddannede svejsere erstattes af ufaglærte i automatisk svejsning.
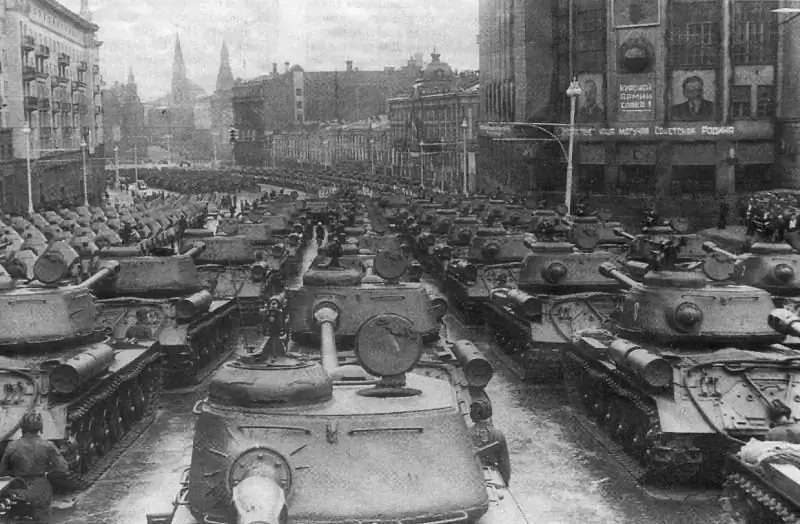
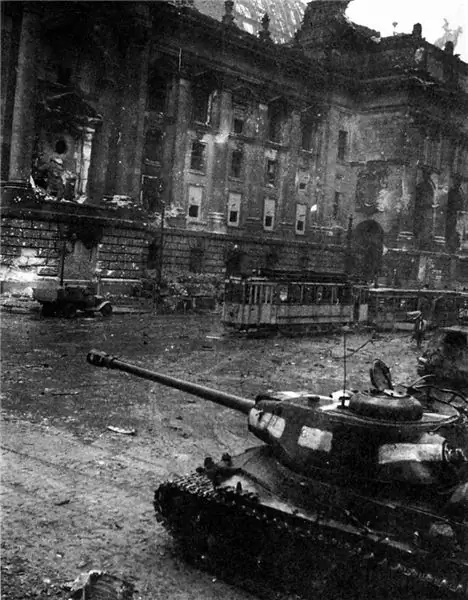
Ural SAG'er
Forsker for den sovjetiske tankindustri, kandidat for historiske videnskaber Zapariy Vasily Vladimirovich fra Institute of History and Archaeology ved Ural Branch of the Russian Academy of Sciences i et af hans værker beskriver meget detaljeret de automatiske svejseenheder, der bruges i Ural til pansrede skrogproduktion.
Den mest udbredte var et angrebsgevær af typen "ACC" med et Bushtedt -hoved. Der var otte sådanne installationer på Uralmash. Trådfremføringshastigheden i denne maskine var afhængig af spændingen i lysbuen. Det krævede 5 enheder, herunder 3 kinematiske elektriske motorer og 1 motorgenerator.
I midten af 1943 blev SA-1000 svejsemaskinen designet til IS-2 tunge tankers behov. Eller en svejsemaskine med en kapacitet på op til 1000 A.
For at mestre produktionen af pansrede skrog til den nye Chelyabinsk tunge tank IS-3, konstruerede ingeniører på fabrikken i 1944 apparatet "SG-2000". Denne maskine blev designet til at arbejde med lav-kulstof svejsetråde med en øget diameter (6-8 mm) og fandt sin anvendelse under fremstillingen af IS-3 tårnet. Installationen havde en dispenser til indføring af en speciel sammensætning (forskellige ferrolegeringer) i svejsesektionen for at deoxidere (gendanne) metallet i den. I alt blev princippet om selvregulering af svejsebuen ved UZTM i 1945 oprettet 9 autosvejseanlæg af tre typer: "SA-1000", "SG-2000", "SAG" ("Automatisk svejsning hoved").
Smukkere end tysk rustning
Resultatet af hele historien med rustningen af tunge IS -tanke var en overraskende hurtig udvikling af en stålopskrift, der overgik den tyske rustning i sine taktiske egenskaber. TsNII-48 modtog et hærdet 120 mm stål, hvis tykkelse om nødvendigt kunne øges til 200 mm.
Dette blev hovedfundamentet for udviklingen af efterkrigsfamilien af tunge sovjetiske kampvogne.