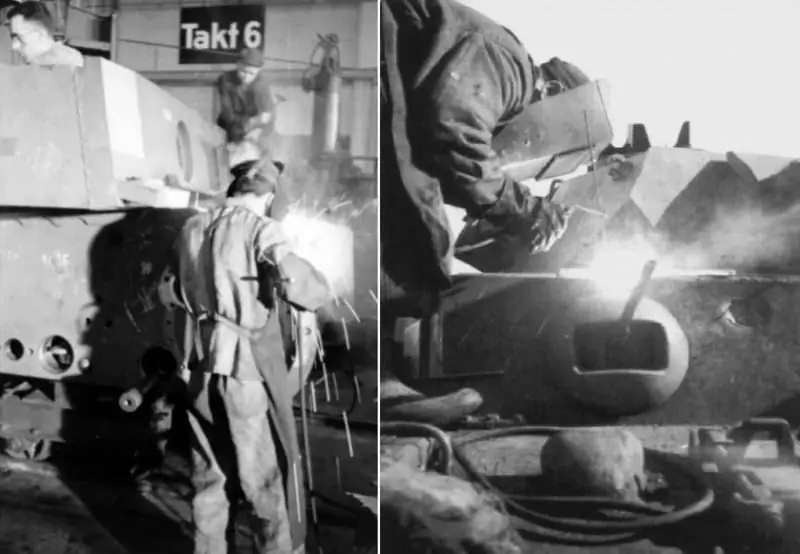
Tysk tilgang
I den første del af materialet om svejseteknologier under den store patriotiske krig blev det nævnt, at en af de vigtigste resultater for sovjetiske teknologer og forskere var introduktionen af automatisering af svejsning af tankskrog og tårne. I Nazityskland blev automatisk svejsning ikke brugt på tankfabrikker. Der var en meget vigtig forklaring på dette - i krigens hovedperiode oplevede Tanksindustrien i Tredje Rige ikke mangel på højt kvalificeret arbejdskraft, herunder svejsere. Og i Sovjetunionen gik der under evakueringen af store virksomheder mod øst tabt personale, der var værdifuldt for industrien, hvilket ikke kun satte kvaliteten af tankmontering i fare, men endda selve produktionsmuligheden. I Tyskland kom det til det punkt, at ved svejsning af skroget til "Panthers" og "Tigers" blev individuelle svejsere tildelt separate sømme! Ingeniør V. V. Ardentov skriver om dette i materialet "Tysk erfaring med skæring af rustninger og svejsning af tankskrog" i "Bulletin of the tank industry" i det sejrrige 1945 -år. Hans arbejde var baseret på undersøgelsen af to pansrede skrogfabrikker i Kirchmeser og Brandenburg. Disse fabrikker havde naturligvis råd til sådan teknologisk luksus i form af separate svejsere til separate sømme indtil de sidste måneder af krigen.
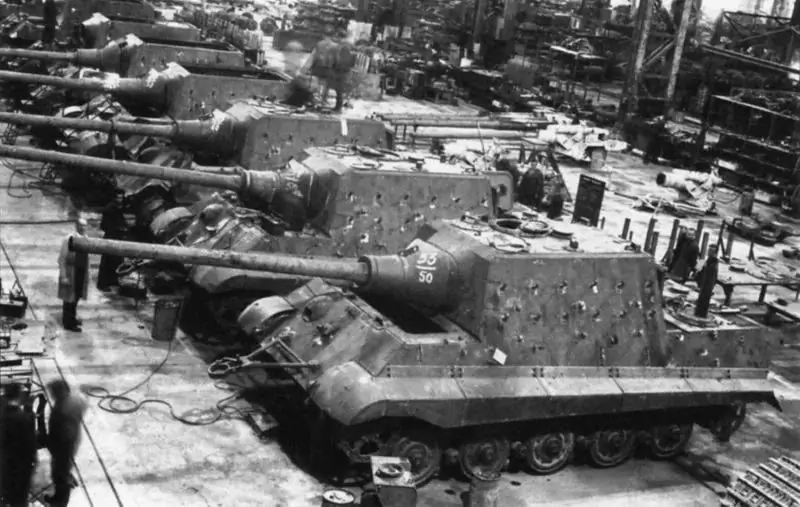
Inden svejsning af skrogene blev panserpladerne skåret, som indtil 1942 blev udført mekanisk. Til afskæring af panserplader til torn-i-torn forbindelser var det meget mere bekvemt at bruge acetylen-iltskæring, som også blev brugt i lignende situationer i den sovjetiske tankindustri. Her var tyskerne foran vores tankbyggere både i effektivitet og i kvaliteten af snittet. Dette er i høj grad resultatet af brugen af værktøjer af høj kvalitet (gasskæremaskiner Messer og Grisheim) med evnen til at finjustere tykkelsen af rustningspladen. Tyskerne brugte også ilt med en høj grad af rensning - mere end 99%. Endelig brugte tyskerne i løbet af at klippe rustningen flere fakler, herunder til affasning. Selve flammeskæringsprocessen var automatiseret - dette gjorde det muligt at fremskynde processen og gøre den meget mere præcis.
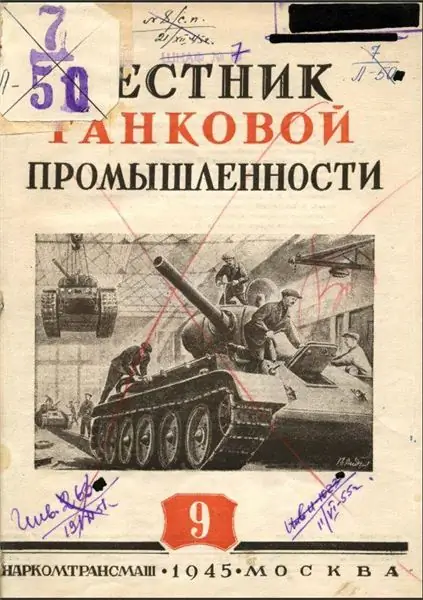
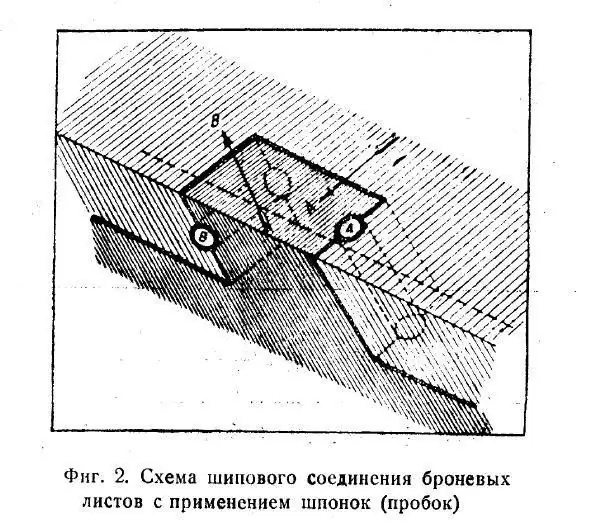
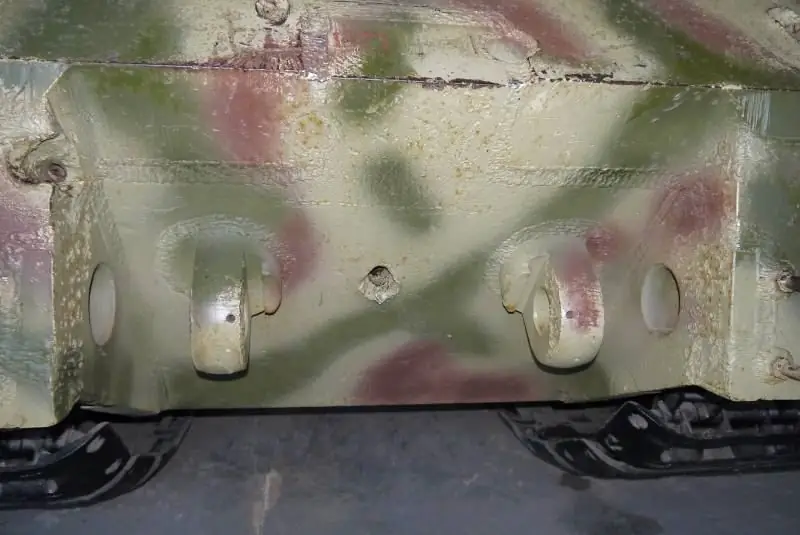
[centrum]
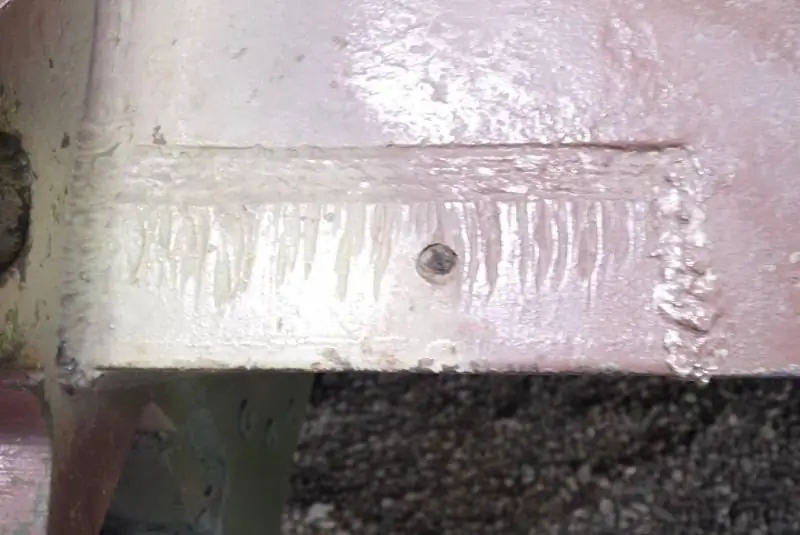
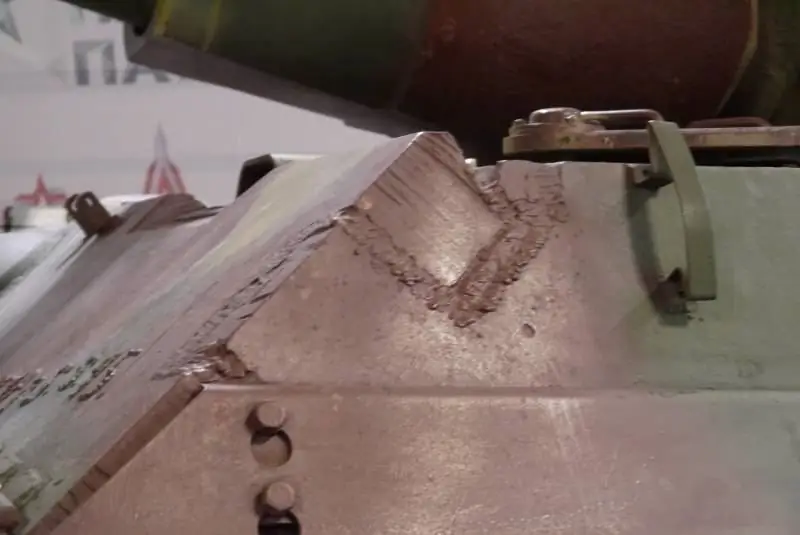
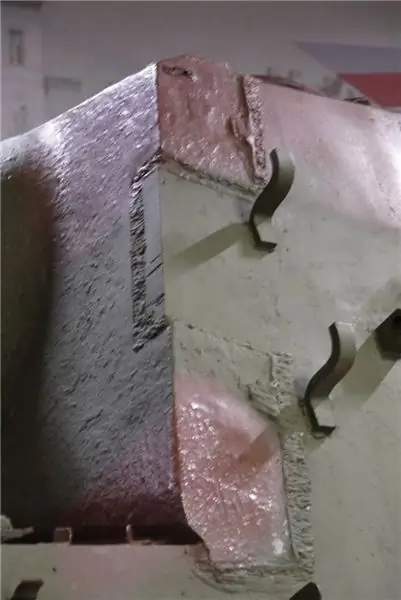
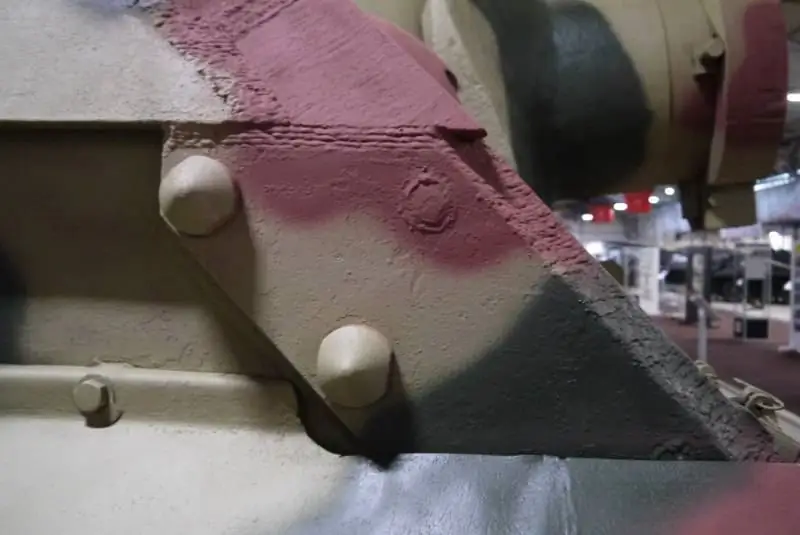
[/center]
Som du ved, var et af kendetegnene ved skrogene på tyske kampvogne fra 1942 spidsforbindelsen af rustningsplader med en rektangulær eller skrå spids. Samtidig var tyskerne ikke begrænset til en simpel artikulation - derudover blev der for styrke indført cylindriske nøgler eller stik i leddene. Især var dette almindeligt på mellemstore kampvogne "Panther", selvkørende kanoner "Ferdinand", tårne af tunge "Tigre" og et par korps af "Maus". Sådanne propper var stålruller op til 80 mm i diameter indsat i samlingerne på pladerne, der skulle samles efter samling til svejsning. Propperne blev anbragt i planet af kanterne på rustningspladernes spids - et par af dem var påkrævet for hver led. Efter installationen af nøglerne blev spidsforbindelsen faktisk et stykke, selv før svejsning. I dette tilfælde blev dyvlerne monteret i flugt med overfladen med rustningen og svejset langs omkredsen af basen. Spidsforbindelsen mellem panserskålene i tankskrogene forbedrede markant den ballistiske beskyttelse af både svejsesømmene og rustningen. Først og fremmest blev dette sikret ved at øge svejsningens samlede længde, der består af separate segmenter, hvilket noget reducerede spredningen.
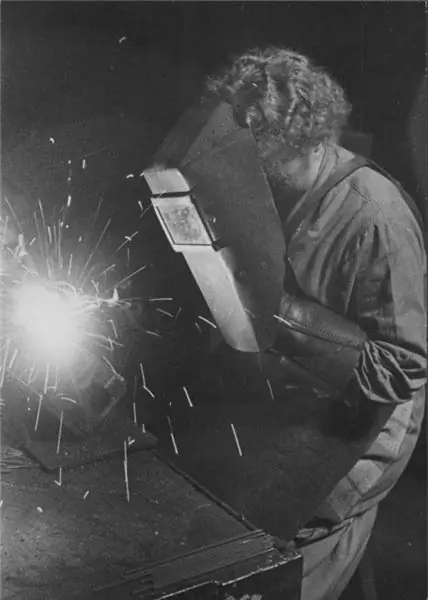
Et af problemerne ved fremstilling af skrog til tyske tanke var fremstilling af udskæringer og huller (f.eks. Til rustningsleddene nævnt ovenfor). Det var umuligt at skære dem med gas, så der blev brugt boring. Til at begynde med var det generelt umuligt at finde en passende boremaskine for stål af kvaliteterne E-18 og E-19, som gennemgik overfladehærdningsproceduren, det ydre lag af rustningen var så hårdt. Ved boring af et hul før slukning, blev der dannet en ujævn slukning i hullets område efterfulgt af deformation og radial revnedannelse. Ja, og der var revner på de tyske tanke og betydelige, og den tyske indsats for at undgå dem vil blive diskuteret senere. Dels blev problemet med ujævn hærdning af rustningen i hullernes område løst med en særlig ildfast pasta, som blev brugt til at dække hullerne, inden den blev sendt til ovnen. Men igen, dette løste kun delvist problemet. Det var først i slutningen af 1944 på Electrothermal Institute i Essen, at dette problem blev løst ved en lokal tempereringsprocedure på rustningens hærdet område. Enheden, udviklet af tyskerne, beskrives i sin artikel af vinderen af Stalinprisen, kandidat for tekniske videnskaber A. A. Shmykov. Materialet blev udgivet i specialudgaven "Bulletin of Tank Industry", som var hemmelig for sin tid og kendt for os, i slutningen af 1945. I efterkrigsårene var Vestniks sider rige på detaljerede analyser af tyske ingeniørers tekniktricks, da der var nok fanget udstyr.
Men tilbage til den lokale udgivelse af rustningen, hvor hullerne blev boret. Grundlaget for enheden var en grafitelektrode forbundet til borestedet, hvorigennem en elektrisk strøm på 220 ampere og en spænding på 380 volt blev passeret. Som et resultat blev rustningen opvarmet til tempereringstemperaturen. Afhængigt af rustningens tykkelse og hulets diameter tog dette fra 7 til 15 minutter. Efter tempereringsproceduren faldt rustningens hårdhed 2-2,5 gange. Det er bemærkelsesværdigt, at den indenlandske industri (herunder tankindustrien) også brugte stålhærdning ved opvarmning med strøm - tyskernes "knowhow" var kun ved brug af en grafitelektrode.
Tyskere og elektroder
Tyskerne brugte også ferie, når de svejste plader af deres rustning med høj hårdhed med et kulstofindhold i området 0,40-0,48%. Dette blev kendt for specialisterne i TsNII-48 (Armored Institute) under krigen, da metallurgiske ingeniører ledte efter opskrifter til at reducere revner i T-34-rustningen. Som det viste sig, frigjorde tyskerne panserpladerne ved temperaturer på 500-600 grader (højferie) og svejste derefter rustningen forvarmet til 150-200 grader i flere passager. Svejsere brugte ikke elektroder med en diameter på mere end 5 mm - svært at tro, i betragtning af tykkelsen af rustningen i tyske kampvogne. Elektroder med en diameter på 4 mm arbejdede ved en strøm på 120-140 ampere, med en diameter på 5-6 mm-140-160 ampere. Denne teknologi gjorde det muligt ikke at overophedes svejseområdet. Det betyder, at der blev opnået en mindre hærdnings- og hærdningszone. Desuden blev sømmen afkølet meget langsomt efter svejsning - alt dette gav i sidste ende tyskerne mulighed for mere eller mindre med succes at håndtere revner på de svejsede led. Derudover blev austenitiske elektroder hovedsageligt brugt, hvilket førte til en høj duktilitet af svejsningen og dens langvarige overgang til en sprød martensitisk tilstand. Ingeniører i TsNII-48 undersøgte meget omhyggeligt funktionerne i den teknologiske cyklus for tankpansersvejsning, hvilket gjorde det muligt med succes at overføre disse teknikker til produktionscyklussen for T-34. Naturligvis havde ingen i tankindustrien råd til en så omhyggelig flerlags anvendelse af svejsesømme i hele tankskroget, den tyske "knowhow" blev kun brugt i de mest kritiske sømme, der er tilbøjelige til at revne.
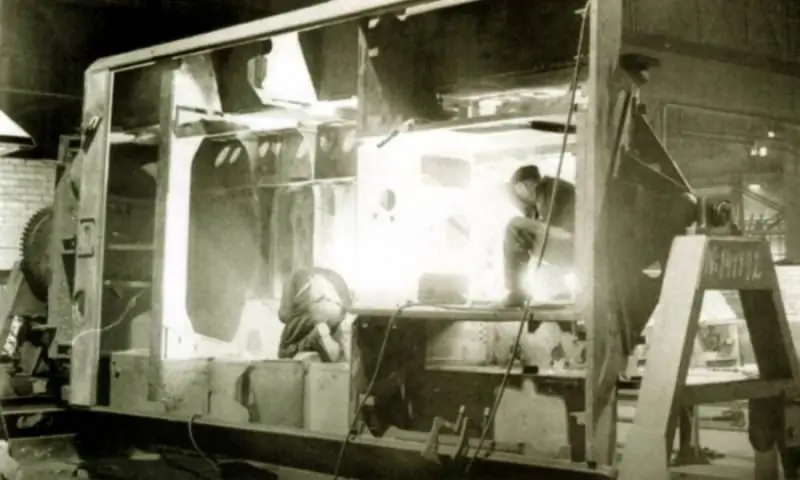
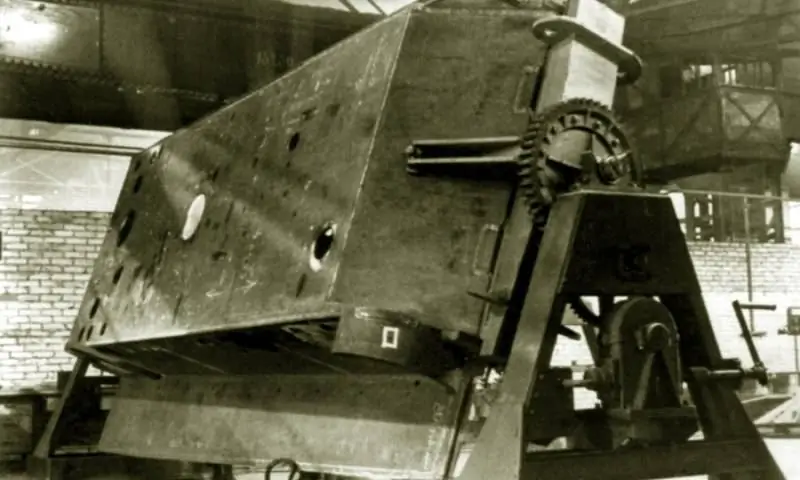
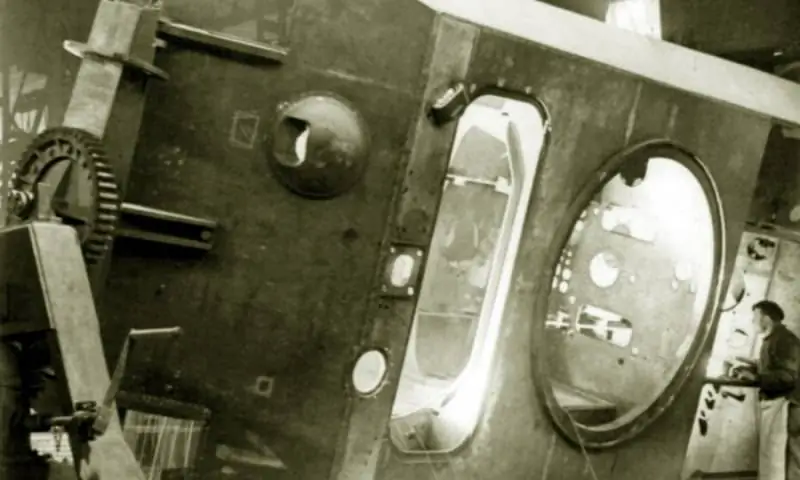
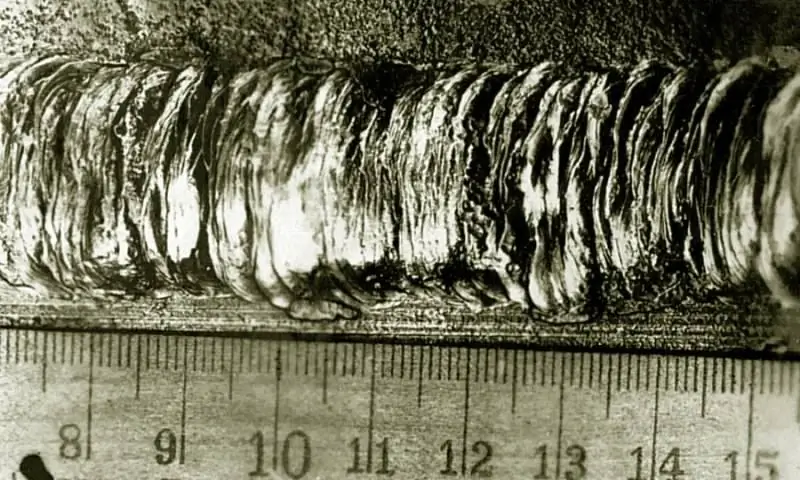
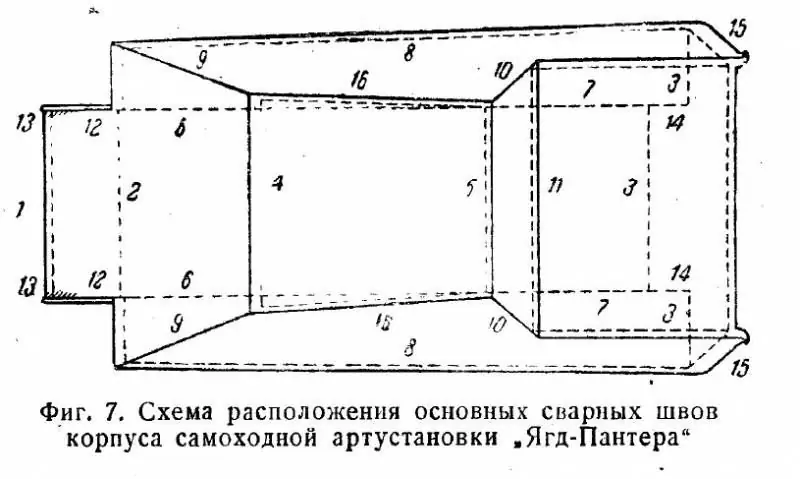
Tyskerne udførte svejsning af tankskrog i forholdsvis behagelige forhold på enorme fliser uden indledende slag (selvom de i nogle tilfælde stadig gik gennem en 5 mm elektrode i hele leddets længde). Tiltteren var en struktur, hvorpå liget på en tysk tank ligesom på et spyd roterede rundt om længdeaksen. Drevet var enten manuelt eller elektrisk. På grund af den høje skæringsnøjagtighed oversteg mellemrummene mellem kroppens dele samlet på rotatoren ikke (i det mindste i krigens hovedperiode) 3-4 mm. Ellers blev der brugt stålprocespakninger. Lange sømme blev brudt af svejsere til flere små og svejset samtidigt i en retning. De lukkende sømme blev også svejset af to svejsere synkront mod hinanden. Dette sikrede den minimale hærdningsspænding af stålet og den mest ensartede fordeling. Ifølge en af legenderne, der blev udtrykt af Alexander Volgin i materialet "Frame for the German Menagerie", var lønnen for svejsere på nogle virksomheder i Det Tredje Rige stykke arbejde - for massen af metal, der var deponeret på tanken.
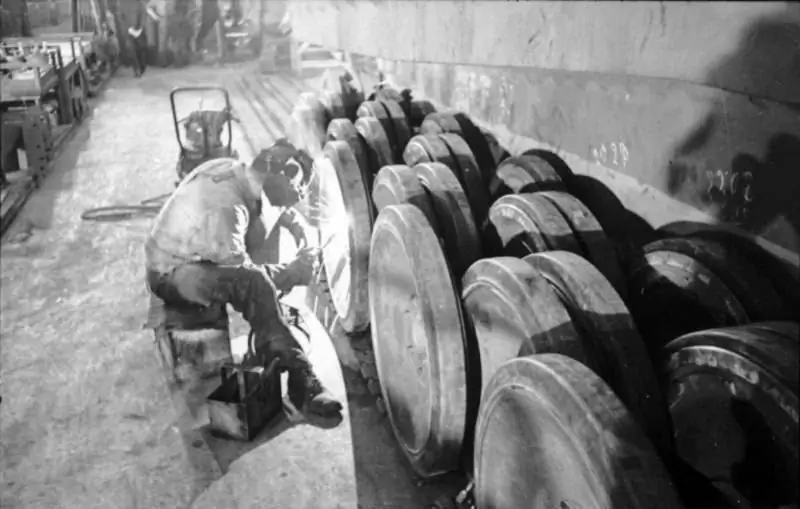
Der er ingen grund til at tale om særlige regler for kontrol af svejsesømme i den tyske tankindustri - der var ingen røntgenstråling, ingen magnetisk fejldetektering, ingen primitiv boring. Og der var revner i sømmene! Hvis de var op til 100 mm lange, blev de formalet og svejset, og hvis mere, blev de smeltet med en lysbue og også svejset. De gjorde også det samme med visuelt opdagede revner i hovedrustningen. Forresten, over tid lykkedes det tyskerne at reducere andelen af revner i svejsede sømme fra 30-40% til 10-20% på grund af nye sammensætninger af elektroder. Også anvendt var vekslen af passager i flerlagssvejsninger med austenitiske og ferritelektroder.